میکرو ماشین کاری لیزری ( Laser micro machining)
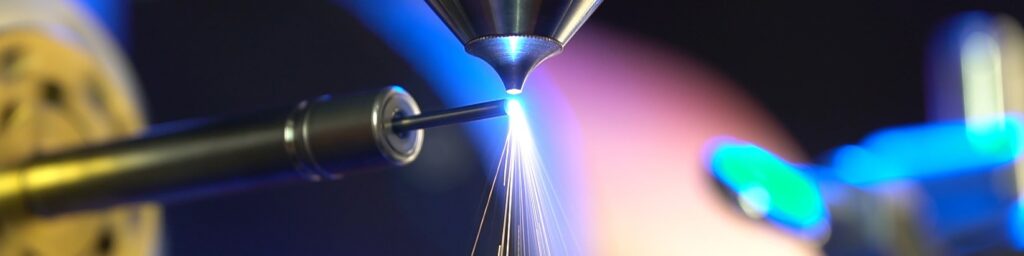
ریزماشین کاری لیزری (همچنین ریز ماشینکاری پرتو لیزر) به معنای ماشینکاری لیزری ساختارهای بسیار ظریف است که معمولاً در مقیاسی بین چند میکرون تا چند صد میکرون است. قطعات ماشینکاری شده همیشه خیلی کوچک نیستند، اما حداقل ساختارهایی (مانند سوراخ ها، شیارها یا الگوهای) روی آنها ساخته شده است. دقت در مقیاس میکرومتر مورد نیاز است (به عنوان مثال برای خطوط برش ریز با زبری کم و مناطق کوچک متاثر از حرارت)، بنابراین اصطلاح مربوط به ماشینکاری لیزری دقیق است. با این حال، ماشینکاری دقیق همیشه بخشی از ریزماشین کاری نیست.
در حالی که روش های کلی برش لیزری، حفاری و غیره در مقالات جداگانه توضیح داده شده است، جنبه های فنی خاص و کاربردهای میکروماشینینگ در ادامه توضیح داده شده است. روشهای معمول ریزماشینکاری عبارتند از: حفاری، برش، فرز، علامتگذاری و ساختاربندی. میکرو حفاری لیزری از نظر تعداد ماشین آلات فروخته شده کاربردی رتبه اول را در صنایع مختلف دارد.
توجه داشته باشید که اصطلاح ماشین کاری به طور کلی فقط برای روش های تفریقی به کار می رود. بنابراین، اصطلاح ریزپردازش لیزری عمومی تر از ریزماشین کاری است، به عنوان مثال همچنین شامل روشهای تولید افزودنی لیزری (به عنوان مثال با استریولیتوگرافی) در مقیاس میکرو و روشهای اتصال میکرو مانند جوشکاری میکرو و لحیم کاری از دسته ریزپردازش لیزری هستند. با این حال، روش های تفریق غالب هستند، و بنابراین اصطلاح ریزماشین کاری بسیار بیشتر از ریزپردازش استفاده می شود.
در مقایسه با ماکروماشینینگ، ریزماشینکاری لیزری با رقابت کمتری با سایر روشهای ساخت مواجه است، در حالی که در عین حال برخی از محدودیتهای معمولی مانند ورودی انرژی نسبتاً بالا برای حذف مواد کمتر مرتبط هستند. به این دلایل و به دلیل تقاضای رو به رشد پیوسته برای انواع زیادی از قطعات مینیاتوری، ریزماشین کاری می تواند یک کاربرد لیزری بسیار مهم در نظر گرفته شود.
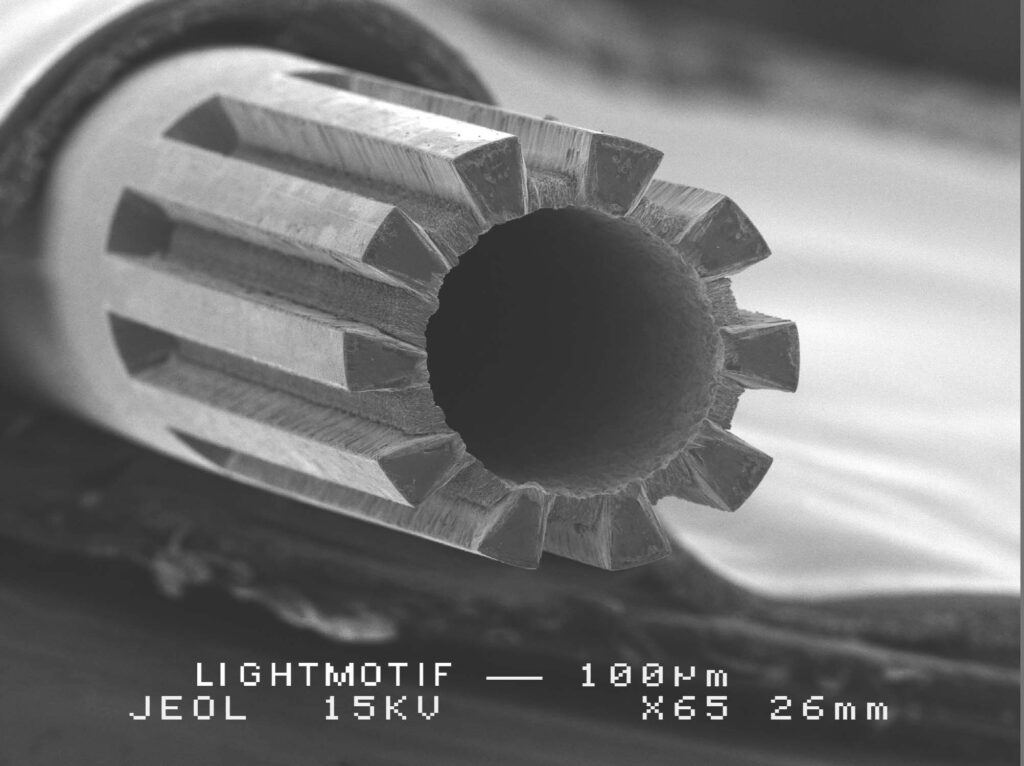
خواص مرتبط نور لیزر در میکرو ماشین کاری
همدوسی فضایی بالا و امکان تولید پالس های فوق کوتاه با شدت بالا برای ریزماشین کاری لیزر ضروری است.
خواص ویژه نور لیزر به ویژه در حوزه ریزماشین کاری مرتبط است، یعنی همدوسی فضایی بالا، پتانسیل تولید پالس های کوتاه یا حتی فوق کوتاه، و شدت نوری بالا که با چنین پالس هایی حاصل می شود. در واقع، سطوح شدت اعمال شده اغلب به طور قابل ملاحظهای بالاتر از عملیات پردازش ماکروسکوپی است، اگرچه میانگین توان درگیر معمولاً کوچکتر است. این به این دلیل است که در حوزه میکرو با پرتوهای لیزر متمرکز تر و پالس های آزمایشی کوتاه تر کار می کند. با این حال، مواردی نیز وجود دارد که انرژی پالس تنها چند نانوژول برای ریزساختار سطوح کافی است.
سیستم های لیزری کاربردی تر، کاربردهای ریزماشینکاری را واقعی تر و رقابتی تر می کنند.
انواع مختلفی از منابع لیزر برای ریزماشین کاری استفاده می شود. بیشتر آنها در این مقاله ذکر شده است. همچنین برای آشنایی بیشتر میتوانید به مقاله کلی تر در مورد لیزر برای پردازش مواد مراجعه کنید. توسعه مداوم منابع لیزر نه تنها به عملکرد لیزر(به عنوان مثال انرژی پالس، مدت زمان پالس، نرخ تکرار پالس) معطوف می شود، بلکه به مفاهیمی نیز مربوط می شود که امکان ساخت سیستم های لیزری را با هزینه کمتر (مثلاً در زمینه فیبر) فراهم می کند. فناوری میکرو لیزر یا لیزرهای ریزتراشه سایر موانع برای کاربردهای عملی، مانند ماشین آلات لیزری حجیم را برطرف میکند. چنین پیشرفتهایی بیش از پیش زمینههای کاربردی قابل دسترس ریزماشینکاری لیزری را گسترش میدهند. در حالی که برخی از معماریهای لیزری کم و بیش تجربی هستند، تنوع روزافزونی از لیزرهای صنعتی به صورت تجاری در دسترس هستند. با این حال، نباید نادیده گرفت که بسیاری از پیشرفت ها در ریزماشینکاری لیزری مبتنی بر توسعه روش های دقیق است، نه فقط منابع لیزر.
محدودیت های وضوح و کیفیت ریزماشین کاری لیزری
در بسیاری از موارد، وضوح فضایی که با روشهای ریزماشینکاری لیزری قابل دستیابی است اساساً توسط شعاع پرتو استفاده شده محدود میشود، که خود توسط پراش در ارتباط با دیافراگم عددی(numerical aperture) قطعات اپتیکی استفاده شده محدود میشود. بسته به شرایط، می تواند منجر به وضوح 1 میکرومتر یا تا حدودی بهتر شود، اگرچه در بسیاری از موارد به دلیل اثرات مخرب مختلف، این حد به طور کامل برآورده نمی شود.
در موارد خاص، وضوح فضایی می تواند به طور قابل توجهی بهتر از پراش محدود باشد.
در شرایط خاص، بر اساس مکانیسم های فیزیکی که در ادامه توضیح داده شده است، وضوح قابل ملاحظه ای بهتر قابل دستیابی است. در سطوح شدت نوری بسیار بالا، برهمکنش نور لیزر با ماده معمولاً از طریق فرآیندهای غیرخطی اتفاق میافتد. به عنوان مثال، جذب غیرخطی در یک شیشه یا یک کریستال شفاف را می توان با جذب چند فوتونی درجه دوم، سوم یا حتی بالاتر آغاز کرد. یک برهمکنش قابل توجه اغلب فقط بالاتر از یک سطح آستانه مشخص برای شدت نوری رخ می دهد، که به این معنی است که انتقال فضایی بین بخش های آسیب دیده و غیر متاثر از ماده می تواند به طور قابل ملاحظه ای تندتر از مشخصات شدت لیزر باشد. بنابراین، فرآیند آغاز شده ممکن است تنها در قسمت داخلی یک نمایه شدت گاوسی شرکت کند. آن ناحیه آسیب دیده می تواند قطری بسیار کمتر از قطر نمایه شدت داشته باشد (شکل 1 را ببینید). با این حال، حتی اگر آستانه برهمکنش به خوبی تعریف شده باشد و انرژی پالس را تا زمانی که فقط درونیترین قسمت به آن آستانه برسد، کاهش دهیم، نمیتوان ساختارهای خودسرانه کوچکی را به دلیل نوسانات ایجاد کرد. از پارامترهای پالس در بهترین حالت، ویژگی هایی با ابعاد بسیار کمتر از 100 نانومتر به دست آمده است.
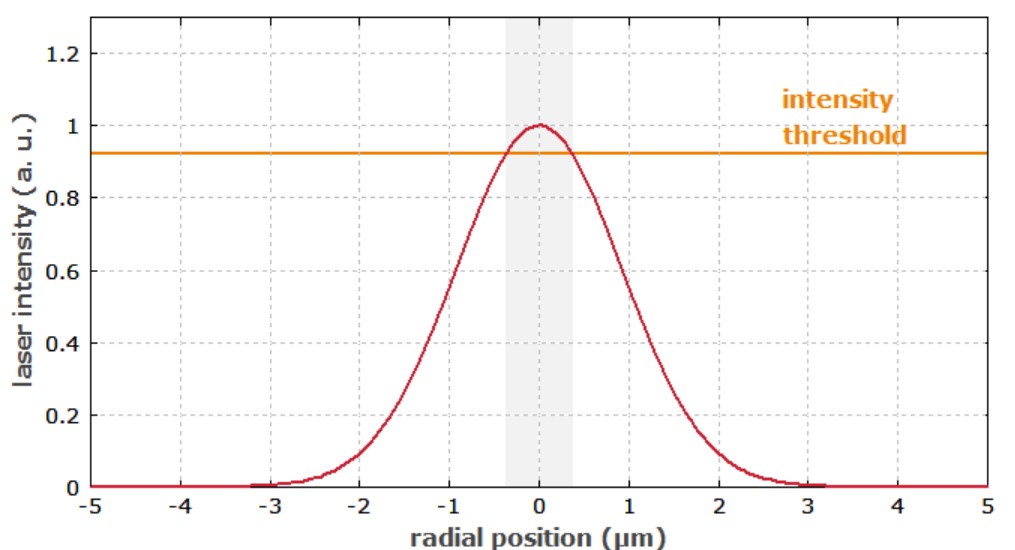
یک رویکرد عجیب تر، استفاده از جلوه های میدان نزدیک(near-field effects) است، یک مثال بر اساس نانوتیپ(nanotip) جهت تقویت میدان لیزری موضعی است. در حالی که چنین روش هایی می توانند وضوح فضایی را بسیار بهبود بخشند، احتمالاً برای کاربردهای صنعتی گسترده مناسب نیستند.
یک رویکرد عجیب تر، استفاده از جلوه های میدان نزدیک(near-field effects) است، یک مثال بر اساس نانوتیپ(nanotip) جهت تقویت میدان لیزری موضعی است. در حالی که چنین روش هایی می توانند وضوح فضایی را بسیار بهبود بخشند، احتمالاً برای کاربردهای صنعتی گسترده مناسب نیستند.
جدای از منابع لیزری، فناوری های اضافی نقش مهمی در ریزماشین کاری لیزر ایفا می کنند. به طور خاص، برای کنترل حرکت به دستگاه های دقیق، سریع و قابل اعتماد نیاز است. اساساً همیشه، فرآیندهای ماشینکاری باید بسیار خودکار باشند، زیرا کنترل دستی در حال حاضر به دلیل دقت مورد نیاز غیرممکن است.
دستگاه های حرکتی با کیفیت بالا که توسط کامپیوتر کنترل می شوند برای ریزماشین کاری ضروری هستند.
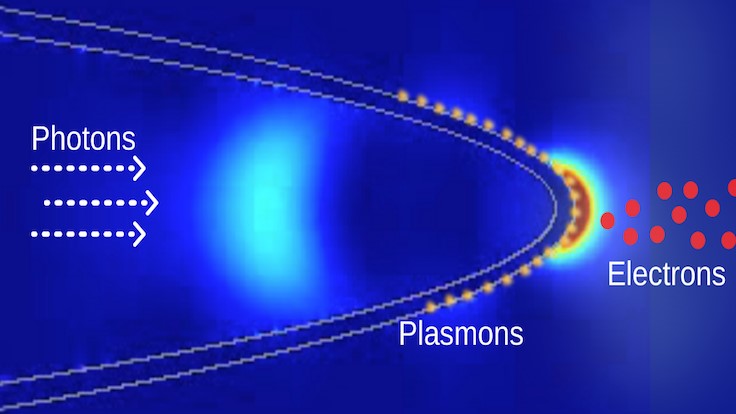
بدیهی است که پتانسیل بسیار بالا برای وضوح بسیار ریز تنها زمانی قابل تحقق است که دستگاه های کنترل حرکت به اندازه کافی دقیق باشند. آنها باید موقعیت های داده شده را در سه بعد با تکرارپذیری خوب و حساسیت کم به اثرات خارجی مانند ارتعاشات به دقت پیدا کنند. معمولاً سیستم های بازخورد مبتنی بر دستگاه های اندازه گیری موقعیت بسیار دقیق مورد نیاز است. برای کاربردهای صنعتی و همچنین برای توسعه اولیه، سیستم های ریزماشین کاری باید به درستی با نرم افزار طراحی مناسب ارتباط برقرار کنند. آنها را می توان به طور کامل در محیط های تولیدی بزرگ ادغام کرد.